移動ロボットの外装部を3Dプリンターで製作!
開発品の動きや完成形イメージの確認がスムーズになり、
省コスト・短納期で開発を実現。
小川優機製作所は、1960年創業以来電子部品事業と受託開発事業の2事業を展開。神奈川県横浜市にある工場で電子部品生産、各種機器の設計製造から研究開発、受託生産までを行っています。長く携わっている電子部品事業は主に大手コネクターメーカー様から製造を請負い、加工生産を行っています。受託開発事業では、サービスロボットを中心とした受託開発を行っており、大手ゼネコン、大学、インフラ企業等のお客様からご依頼頂いています。保有しているプレス機、マシニングセンター、旋盤、フライス、3Dプリンターを活用し、受託開発・量産に入るまでを手がけております。
- 所在地:
- 神奈川県横浜市
- 主な業務:
- ・電子部品生産
- ・各種機器の受託開発事業
- URL:
- https://www.ogawayuki.com/
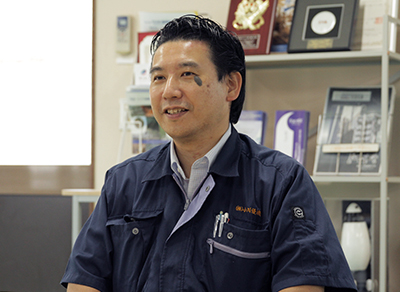
設計や製作のスピード感を早めるのに役立つ3Dプリンター
電子部品事業と受託開発事業の2事業を展開していますが、特に受託開発事業では新しいアイデアによる新規機器開発や特殊機能を追求する各種ロボットの開発研究など、多様な分野の試作品の開発から生産まで行っています。動きのイメージ、完成形のイメージをお客様とすり合わせ、認識の違いを減らすことが重要ですが、3Dプリンターを活用し、短納期での開発を行っています。
さらに工数がかかる表面研磨・塗装の後処理まで対応してもらえた
3Dプリンターで製作した部品(一例)
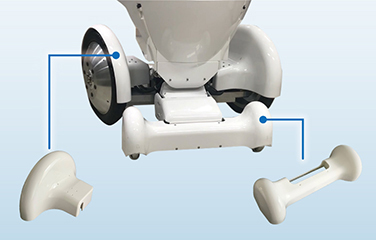
移動ロボット車輪部
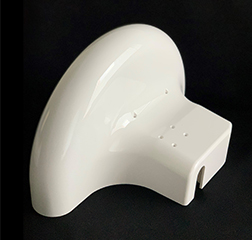
車輪カバー①
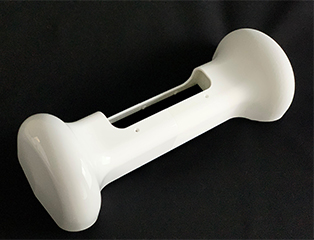
車輪カバー②
導入した機器/サービス
自社の設備では造形できない大型サイズ、複数パーツで構成されているロボットの外装部品製造を短納期で行うため、複数社の出力サービスを検討した結果、費用と納期、複数パーツを全部まとめて対応してもらえたためにリコーの「3Dプリンター出力サービス」を利用しました。
お客様インタビューCustomer Interview
株式会社 小川優機製作所
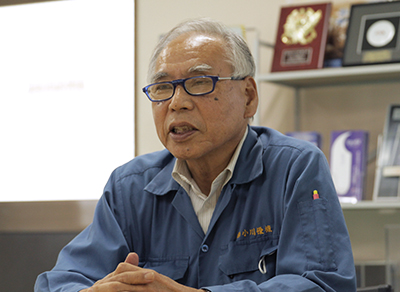
- 代表取締役 会長
- 小川 安一様
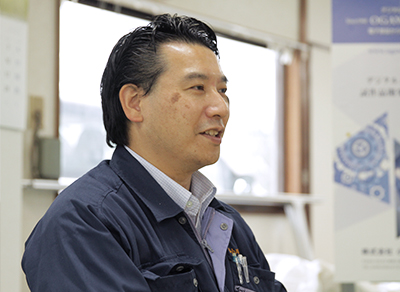
- 代表取締役 社長
- 小川 壮一様
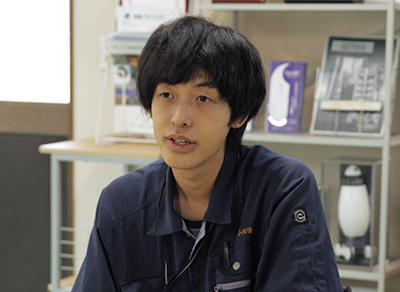
- 開発グループ 主任
- 佐藤 友哉様
背景・課題
曲面が多く、薄肉・大型のロボットの外装部の製作必要
明治大学(理工学部機械工学科ロボット工学研究室)様の「次世代ロボット中核技術開発プロジェクトにおける新規開発」に参画させていただくことになり、移動ロボットを約1年で設計・製造をすることになりました。開発を進める中で、明治大学様と認識を合わせるために試作品を作る必要がありましたが、移動ロボットの外装部は曲面が多く、また大型の薄肉パネルのため、切削で製作した場合は複数パーツを貼り合わせて作る必要があります。その場合、構造的に弱い部分が出てきてしまうので、納期と安全性の観点から切削よりも3Dプリンターで製作することにしました。しかし今回は800㎜を超える大型の造形が必要であったため、自社で保有している3Dプリンターでは造形できないという課題がありました。
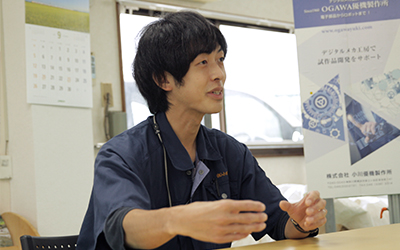
出力サービスの活用について
省コスト化・短納期・後加工の手間削減が3Dプリンター出力サービス活用により実現
10年前に3Dプリンターを購入し、試作品や社内の治具等の製作のために現在は2台保有しています。動きや完成形のイメージは3D CADで説明するよりも、試作品を手に取って触っていただいた方がお客様のイメージがつきやすく、認識のずれも減らすこともできます。また開発スピードも1~2か月かかっていたものが約2週間と大きく短縮できたこともありました。
今回のプロジェクトでも関係者とイメージ共有をするために試作品を作ることになりましたが、移動ロボットの機構の設計が完了した後に外装パネルを作っていくスケジュールで進めていましたので、3Dプリンターで作るパーツについては、短納期での製作が必要でした。例えばロボットの車輪部の場合、車輪の位置やつけ方が決まった後で外装を被せていきます。そのため外装部については最終段階で製作を依頼しないとならず、また他にも多くのパーツの試作もありましたのでタイトなスケジュールで進めていました。大型サイズ、多くのパーツを製作することから、外部の3Dプリンターで造形を行ってもらえる業者3社に見積り依頼し、費用・納期の面から「リコー3Dプリンター出力サービス」への依頼を決めました。見積依頼後すぐに担当技術者と相談でき、最適な造形方式や造形材料の提案や、納期に間に合わせるために1回の造形でどのように配置して複数パーツを造形するのがよいのかを考慮して造形してもらいました。このような点はやはり造形のテクニックになるので技術者に相談できてよかったです。また一番良かったのは、後処理まで対応してもらえたことです。外装パネルのため、表面研磨・塗装を社内で対応しようと思っており憂鬱だったのですが、リコーさんに対応してもらえて非常に助かりました。
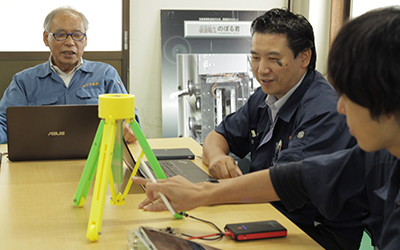
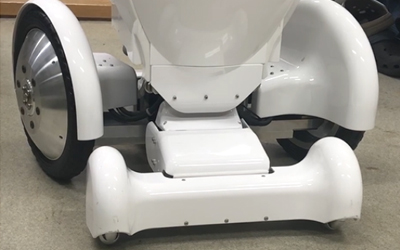
移動ロボット車輪部
3Dプリンター活用メリット
一体造形により組み立て工数を削減さらにスムーズなロボット走行を支える剛性を持たせた
外装パネルが完成
マシニングセンタ等の装置も保有していますが、3Dプリンターを活⽤することで試作品をすぐに作りお客様と動きや完成形のイメージのすり合わせができ、認識の違いを少なくすることで打合せ回数が減り、開発の納期短縮ができているのでとても役⽴っています。その他のメリットとして3Dプリンターは、3D CADで設計したデータをそのまま形にできるため、思い通りの形状で設計ができ、製作が楽になるというメリットもあります。また複数パーツを組み合わせることなく⼀体造形が可能になるというメリットもありました。従来はいくつかの部品を組み合わせて動く構造物や、複雑な形状の⽴体物の場合は複数の部品の組み合わせ、貼り合わせを⾏っていました。しかし3Dプリンターで⼀体造形で製作することにより、組み⽴て・貼り合わせの作業が不要になり、コスト削減や納期短縮ができています。さらに今回の移動ロボットの⾞輪部カバーの場合、特に外装パネルを貼り合わせると歪みが⽣じて途中で割れてしまう懸念がありましたが、⼀体造形で製作したことにより、スムーズなロボット⾛⾏を⽀える剛性を持たせた外装パネルができました。
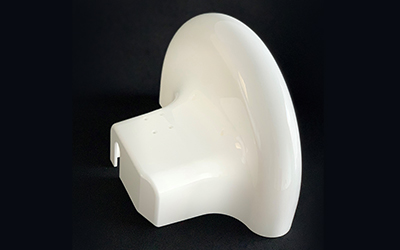
車輪カバー①
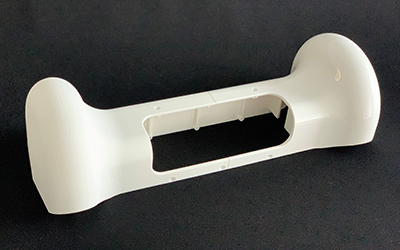
車輪カバー②
今後の展望
軽量化が求められる構造部品など、現状は切削で対応している製作を今後は3Dプリンターで造形していくことも検討しており、ラティス構造など切削では製作が難しかったような形状も考えています。現状は樹脂の3Dプリンターを活用していますが、いずれは金属やカーボン等の3プリンターも活用したいと考えています。またフルカラーの造形や樹脂型で対応していた10~20個程度の小ロット生産など3Dプリンターは使い方次第で様々な用途で使用できるので、今後も活用範囲は増えていくと思います。