免震橋梁の開発に向けた研究に3Dプリンターを活用!
3Dプリンター出力サービスを活用する事で、
コストを抑え免震部材のモデルを製作し、実験を実施
早稲田大学 創造理工学部 社会環境工学科 秋山研究室は2011年度に創設された研究室です。コンクリート系インフラ構造物,あるいはそれを含む道路や鉄道ネットワークの安全・安心を確保するための研究を実験的、あるいは解析的アプローチにより実践しています。
(担当分野:コンクリート系インフラ構造物の耐震問題や次世代耐震構造の開発,あるいは維持管理や長寿命化技術の高度化)
- 所在地:
- 東京都新宿区
- 主な研究テーマ:
- (1) ダメージフリーインフラ構造物の開発(超免震構造・高耐力構造)
- (2) 地震・腐食環境下にあるインフラ構造物のライフタイム信頼性解析
- (3) 点検・検査情報を活用したコンクリート系橋梁の余寿命評価
- (4) 道路ネットワークの地震リスク解析
- (5) 2011年東北地方太平洋沖地震による道路橋・鉄道橋の被害分析・各種機器の受託開発事業
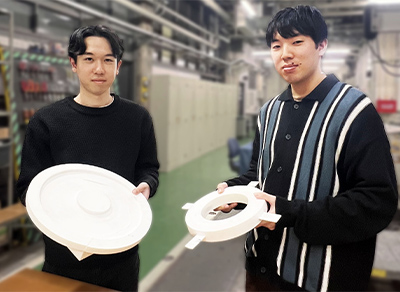
大学の研究で3Dプリンターを活用し、既存工法では時間もコストもかかる複雑形状の免震部材である摩擦振子を造形
3Dプリンターで製作した部品(一例)
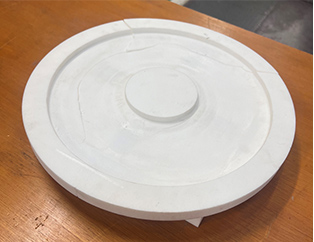
滑り面
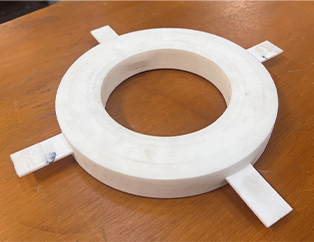
摩擦振子
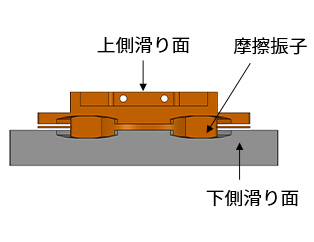
断面図
導入した機器/サービス
大学の研究室で橋梁などの耐震設計の研究を行っており、摩擦振子型免震橋梁の実験で使用する実験供試体のパーツの一部をリコーの「3Dプリンター出力サービス」に依頼し造形しました。
お客様インタビューCustomer Interview
早稲田大学 創造理工学部 社会環境工学科 秋山研究室
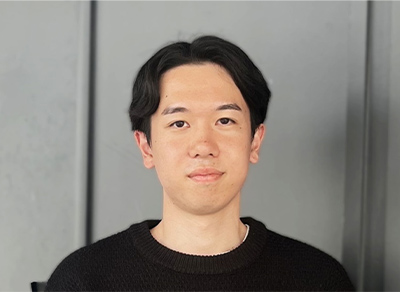
- 臼井 駿矢様
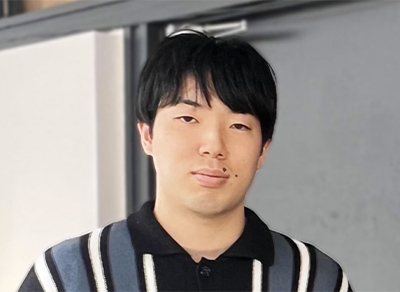
- 小林 慎太郎様
背景・課題
秋山研究室では暮らしを支えるインフラ 構造物の安全・安心を確保するために超免震構造・高耐力構造、長寿命化技術の研究や開発を行っています。研究を進める上で摩擦振子型免振構造の開発に向けて震動実験を行いますが、これまではその実験で使用する滑り面と摩擦振子というパーツを金属で製作していました。しかし摩擦係数が大きく、また滑り面は凸形状で表面には複雑な角度をつける必要があるため製作コストが高くなっておりました。そのため、金属以外の他の材料や製作工法にて製作ができないかを検討していました。その後、過去に卒業した先輩方が同様のパーツをリコー3Dプリンター出力サービスに3Dプリントの依頼をしていたことを知り、今回相談することにしました。
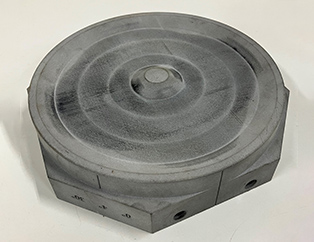
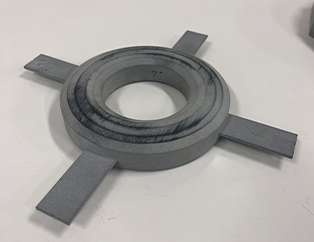
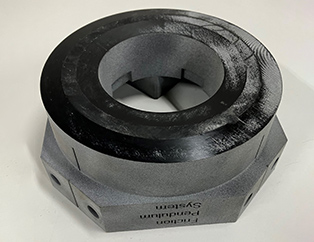
過去に製作した滑り面および摩擦振子
出力サービスの活用について
3Dプリンターが初めてでも専任技術者のサポートにより安心して発注
過去に先輩方がリコーさんに発注した滑り面と摩擦振子の造形物は品質もよく、震動実験も問題なく出来ていましたが、今回はさらに発展させた研究を行うために過去に3Dプリントしたサイズよりも大きく、より強度が必要な滑り面と摩擦振子を製作する必要がありました。私達は3Dプリンターを初めて活用するため、3Dプリンターで製作したパーツの強度やモデルデータ通りに形状が再現ができるのかが分かりませんでした。しかしリコー3Dプリンター出力サービスでは依頼したデータを単にそのまま造形するのではなく、造形依頼前に専任技術者に相談することができ、懸念点や希望する条件で造形ができるのか、造形材料は何が良いのか等を教えてもらうことで理解、納得した上で発注することができました。また滑り面のパーツは角度を細かく変化させた複雑な形状を含んでおり、モデルデータ通りに造形ができるのか不安でしたが、実際に造形する際にはそこに配慮した姿勢で造形してもらい希望通りに造形できたのも良かったです。
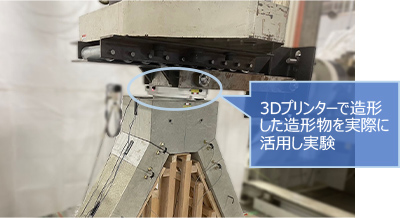
3Dプリンター活用メリット
複雑な形状、自由度の高い形状のパーツを作るには、3Dプリンターがとても有効的で安価に製作することが実感できました。金属で製作していた頃は削りで製作していましたが、滑り面のパーツは表面に数種類の角度を設けた形状であるため製作費がとても高くなります。そこで金属ではなく樹脂材料で製作ができないかを検討していました。当初は摩擦係数が小さいフッ素樹脂(テフロン™)への置換えを検討していましたが、3Dプリンターで対応ができ、また安価に造形ができるナイロン材料を選択することにしました。3Dプリンター造形サービスの場合は2次元の図面なしで依頼できるのもとても助かりました。
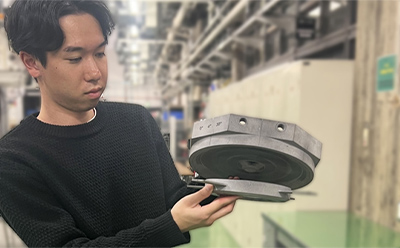
今後の展望
今回、リコー3Dプリンター出力サービスに造形を依頼し、滑り面と摩擦振子の2パーツを作成し実験を行うことができました。しかし実験中、滑り面に大きな力がかかった際に、滑り面の一部が破損してしまいました。実験において滑り面に対してかかる荷重を、事前にシミュレーションすることが最善ですが、材料が有する摩擦係数の測定、および複雑な形状における解析は困難です。そのため、今後は解析手法の改善に取り組むとともに、実験においてはさらに強度を持たせるよう造形したいと思っています。リコー出力サービスの技術者から3Dプリンターの特徴を活かす事で、さらに強度を持たせた構造に改善する提案ももらいましたので、今後検討をしたいと思います。
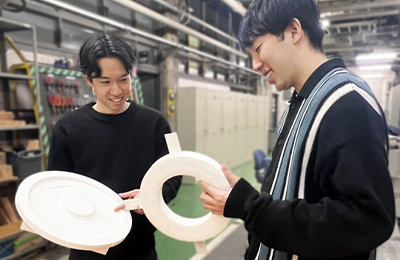